As part of recent investments made in the company, Diesel Technic has further enhanced the Diesel Technic Quality System (DTQS). Extended testing and state-of-the-art measuring options under laboratory conditions as well as an own electronics test laboratory ensure future-proof conditions for quality assurance.
Quality and safety play a particularly important role when it comes to automotive parts. As an international supplier of automotive parts and accessories, Diesel Technic knows that in addition to ensuring its products are reliable, it is also of key importance to keep developing them. In order to be able to keep offering spare parts of the highest and guaranteed quality, the Diesel Technic Quality System cannot afford to remain static.
The DTQS is the guarantee of a consistently high level of quality as well as a guarantee of the products of the DT Spare Parts and SIEGEL Automotive brands. It is therefore also a core value for the Diesel Technic company.
What does the DTQS department look like at company headquarters in Kirchdorf, Lower Saxony? Over 50 experienced employees dedicate themselves to the various areas of their work every day. The working areas with the test laboratories extend over an area of around 1,000 m².
In-house test centre
In the DTQS test centre, performance and lifetime tests are carried out on highly specialised test systems and test benches developed in-house. This makes it possible to simulate situations of application in the vehicle and carry out performance tests. In addition, durability tests are designed and carried out under laboratory conditions. These are often verified by field tests in order for the environmental influences and real installation situations to flow into the development process.
The basis for the tests is always the corresponding OE/OEM samples, often also the corresponding counterparts. There are testing options for a wide variety of product groups – for example, for water- and oil pumps, power steering pumps, brake valves, window regulators and motors, air spring bellows and many more – and these are constantly being developed.
Trained specialists then assess the results and, if necessary, initiate further processes for product development and optimisation. In addition to these laboratory product tests, practical tests with test fleets from competence partners are carried out on a regular basis. This feedback is also continuously incorporated into sustainable improvement of the quality of the brand products.
Measuring room for coordinate measuring technology
Various measuring systems and measuring machines – which work under the most stable conditions in the Class 1 measuring room in accordance with VDI/VDE 2627 – ensure highly accurate and reproducible measurement results. In addition to calibrated measuring machines, coordinate measuring technology also require a stable climate. This is generated in the measuring room under the strictest specifications and rules. Only then can reliable measurement results in the µ range (0.001 mm) be achieved. This in turn has a decisive influence on the quality of the parts of the engine and transmission system.
Electronics test laboratory
In addition to standard tests such as testing of window regulator motors and headlights, testing options for multifunctional articles – such as door control modules – are also developed in the e-lab, and all the relevant functions tested.
For complex items from the BUS system, test methods are developed that are closely linked to the real application situations and communication flows in the vehicle.
Keeping an eye on market developments, it will remain the core competence of Diesel Technic to develop branded spare parts with guaranteed quality for the various requirements and to ensure the supply of more than 41,000 products from its spare parts portfolio worldwide.
Diesel Technic Quality System (DTQS) as guarantee of quality
DIESEL TECHNIC
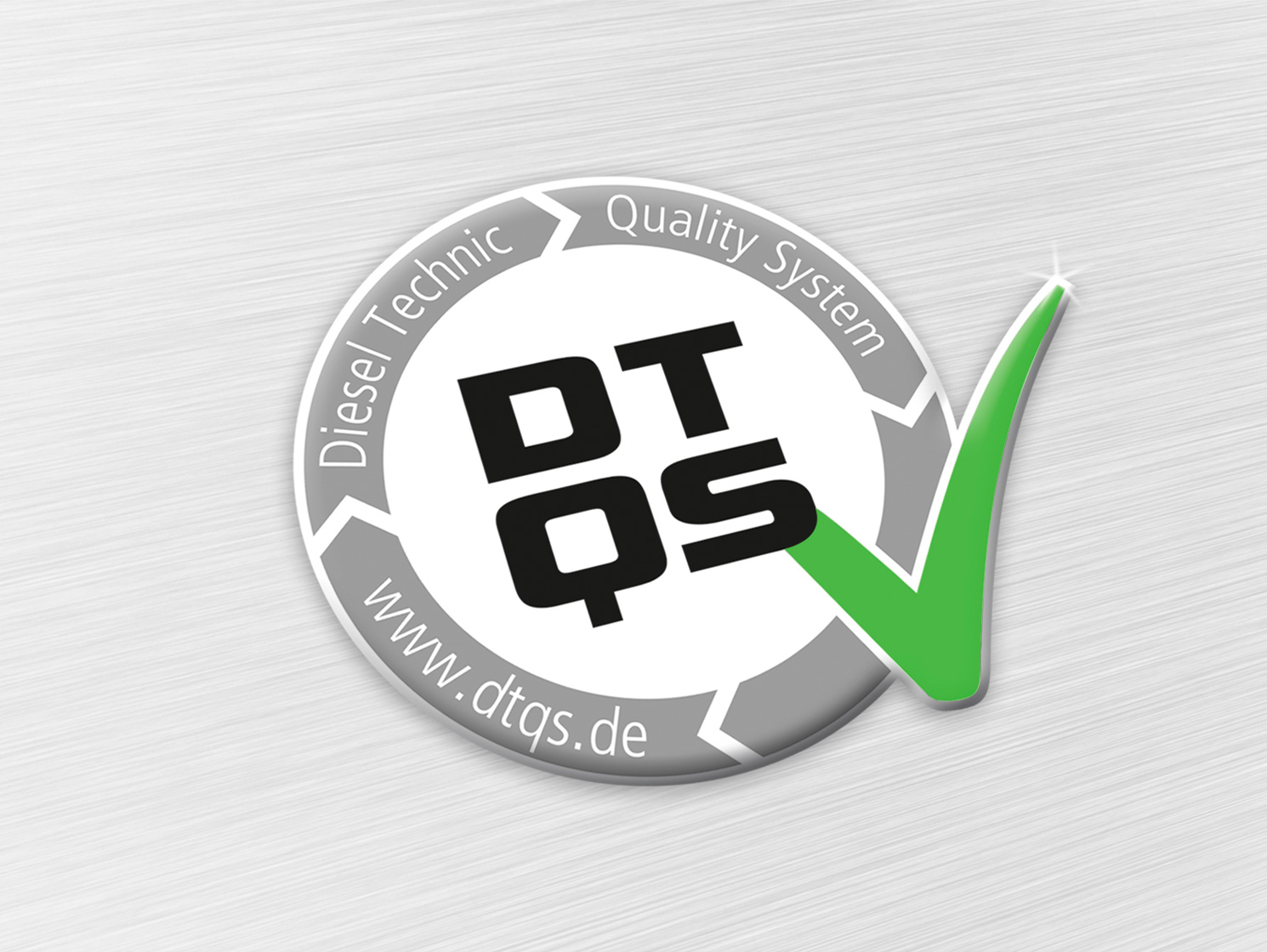